Aumente a produtividade dos processos e pessoas, reduza os desperdícios e os ciclos operacionais e financeiros com o suporte de uma Consultoria Lean Manufacturing.
Consultoria Lean Manufacturing
O QUE VOCÊ IRÁ ENCONTRAR NESTA PÁGINA:
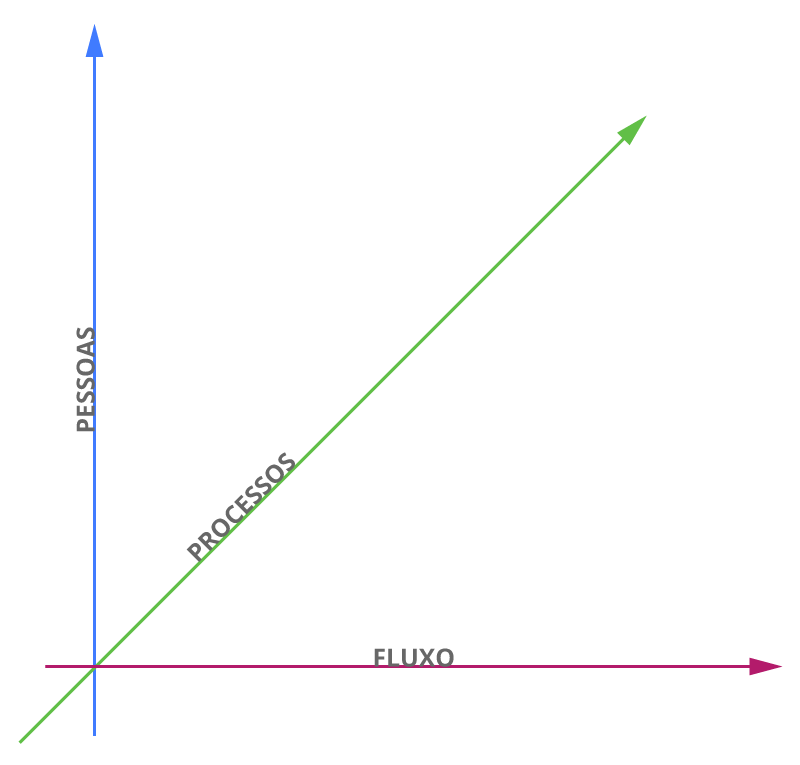
O QUE É LEAN?
Lean é um sistema de trabalho que otimiza FLUXO, PROCESSOS e PESSOAS.
Requer menos fluxo de caixa, mas que exige em contrapartida um maior envolvimento das pessoas no uso de conceitos e ferramentas para economizar tempo e recursos.
Acesse nosso Linkedin, conheça um pouco mais sobre a Konrad!
O Lean reduz os custos dos processos e o ciclo operacional, que é o intervalo de tempo entre a compra da matéria-prima, seu processamento, entrega e o recebimento.
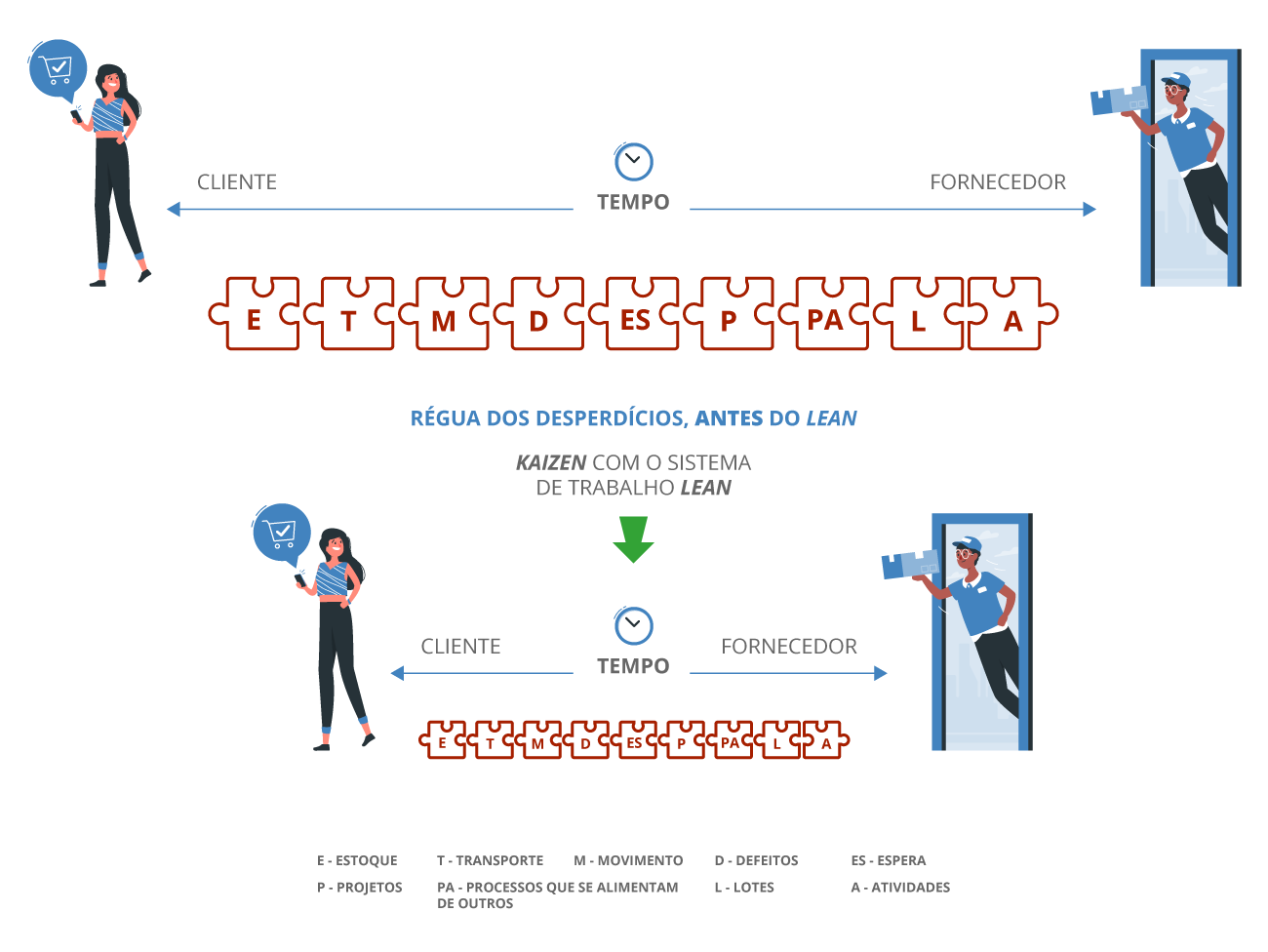
Lean significa “enxuto”, então Lean Manufacturing é entendido como “Produção Enxuta” pois busca reduzir, ou no sentido figurado enxugar todo tipo de desperdício.
A eliminação do desperdício não tem limites, é como uma toalha molhada, não importa o quanto você a torce, sempre sai água.
LEAN: DESPERDÍCIOS
O Lean reconhece que os desperdícios que ocorrem ao longo dos processos são como vazamentos numa estrutura hidráulica que diminuem o lucro final.

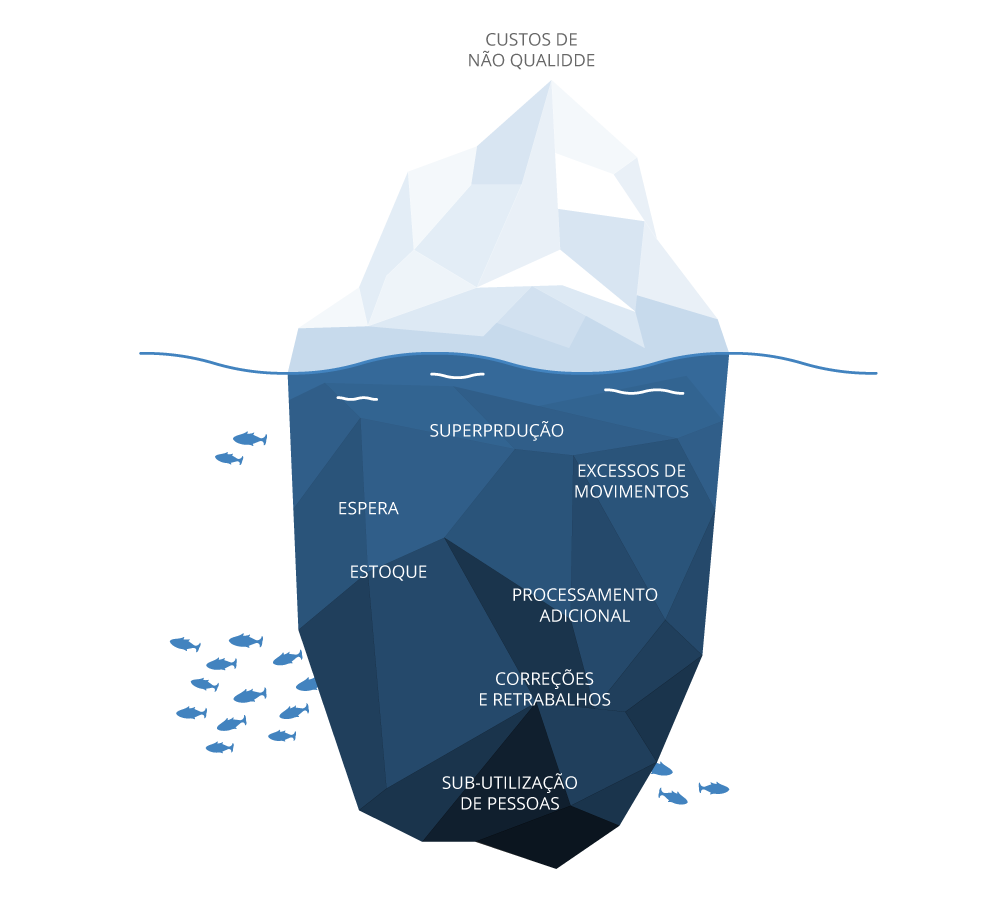
LEAN: CUSTOS DE NÃO QUALIDADE
O Lean reconhece que os custos da não qualidade como falhas e defeitos em atender aos requisitos dos clientes são somente a ponta do iceberg de todos custos que não agregam valor.
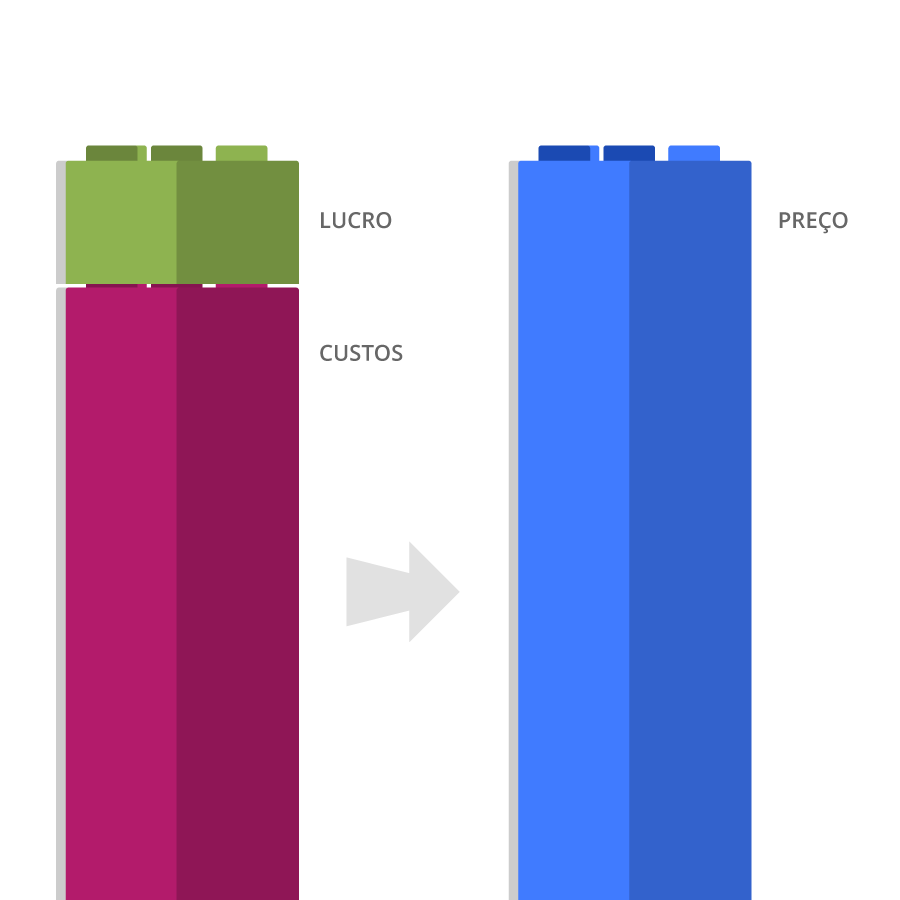
No pensamento tradicional: Custos + Lucro = Preço
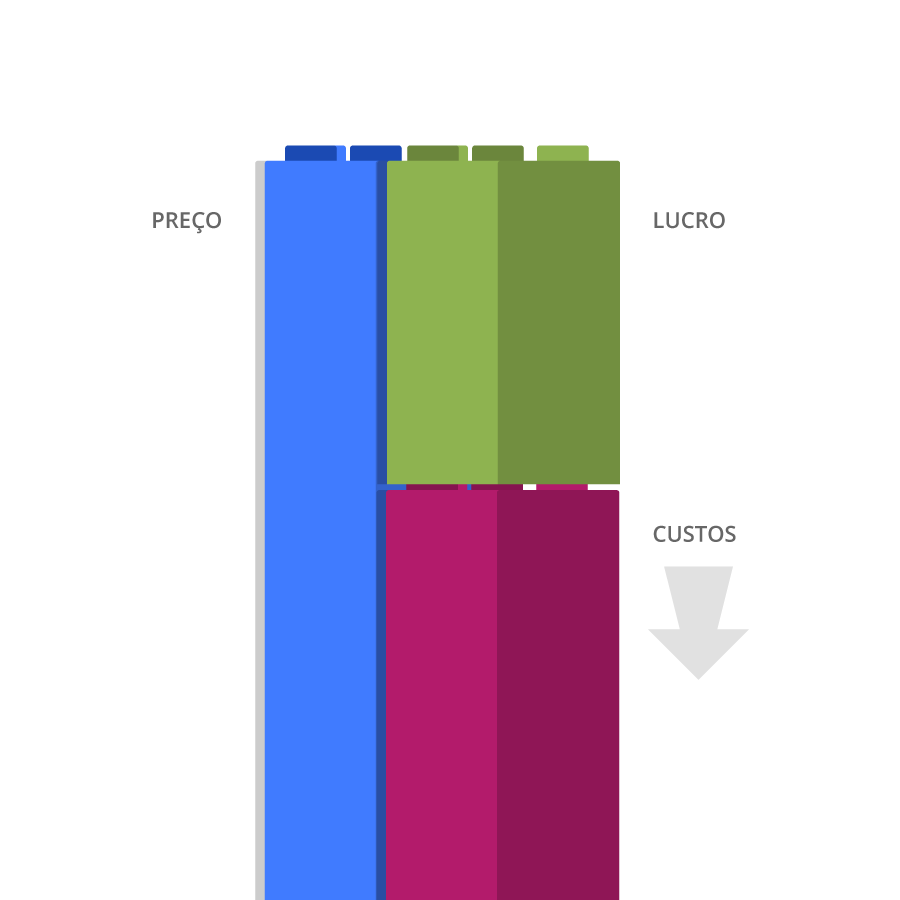
O Lean entende que o preço é ditado pelo mercado, então: Preço – Custo = Lucro!
(O que justifica uma perseguição continua dos desperdícios).
Lean requer menos braços e mãos, e mais cabeças!
CONSULTORIA LEAN : APLICAÇÕES TÍPICAS
LEAN NA INDÚSTRIA METAL-MECÂNICA E ELETRO-ELETRÔNICA
O Lean na indústria metal-mecânica e eletro-eletrônica busca fazer mais com menos e obter resultados melhores aos olhos dos clientes e para as organizações:
- Reduzindo os erros de fabricação e montagem;
- Reduzindo os estoques;
- Reduzindo o tempo de entrega, entre outros inúmeros benefícios.
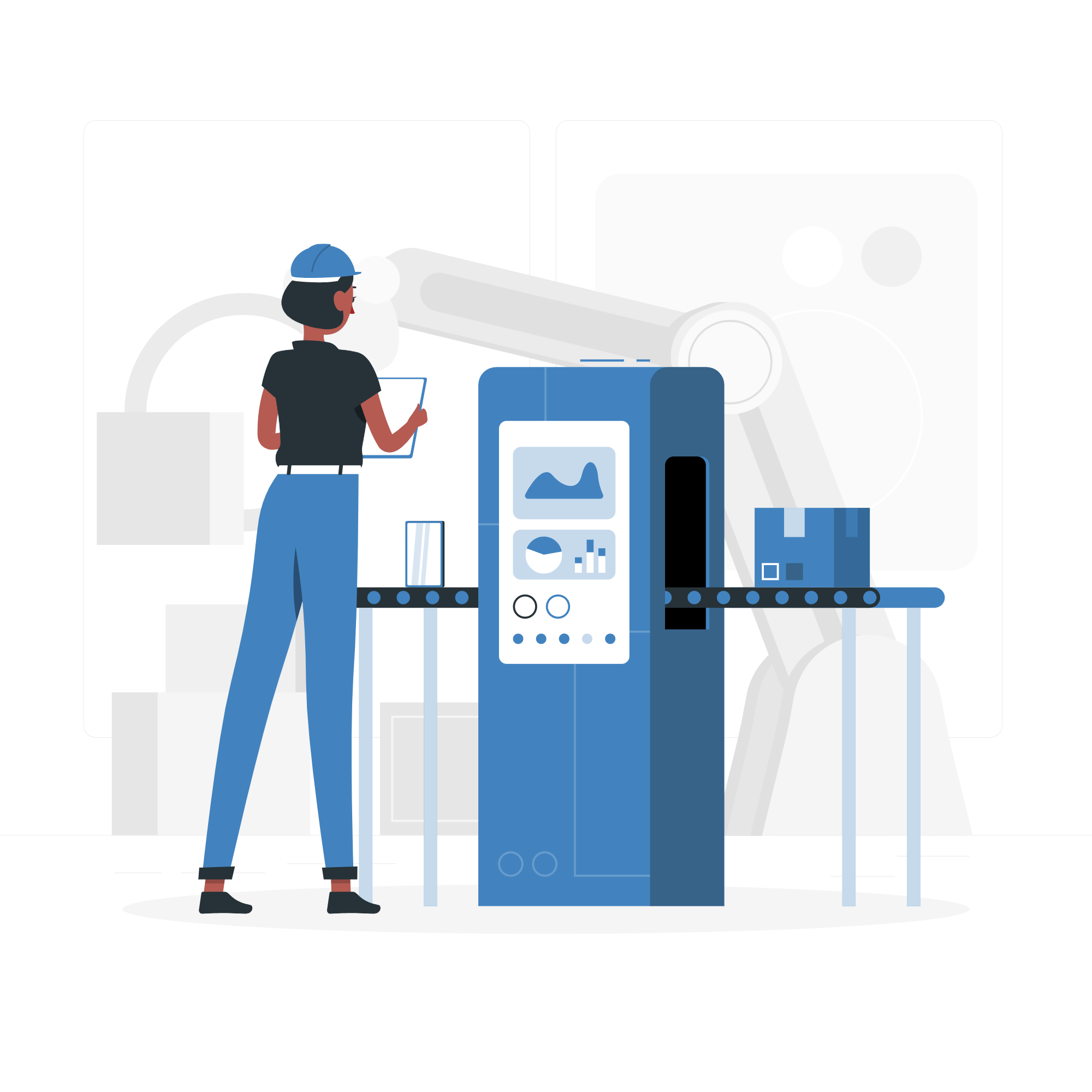
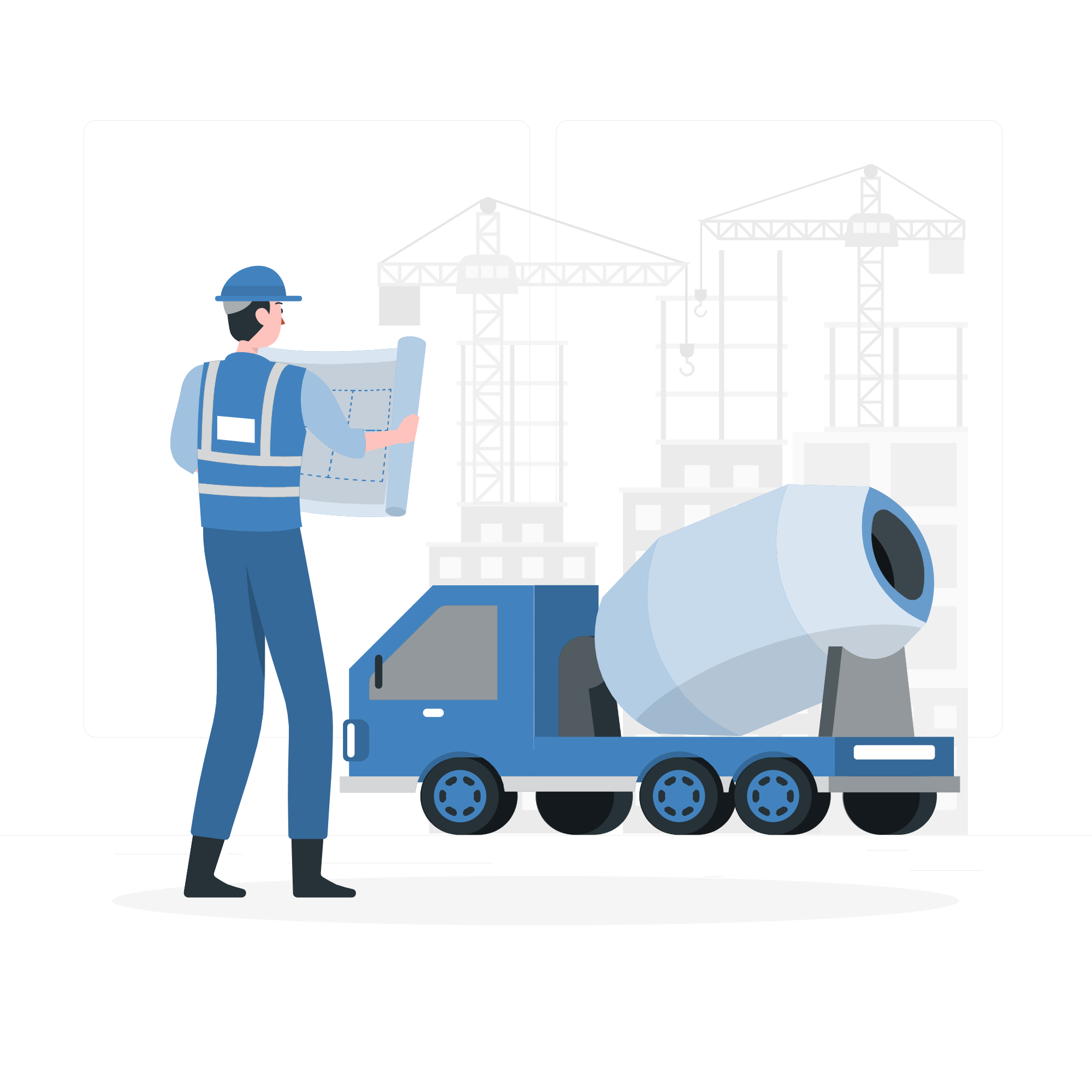
LEAN NA CONSTRUÇÃO CIVIL
A aplicação do Lean na construção civil visa otimizar os processos do projeto à incorporação e solucionar os seus principais problemas:
- Lead time elevado, pois os edifícios e conjuntos habitacionais levam em média 3 anos para serem incorporados;
- Desperdícios e retrabalhos durante a construção em torno de 30% do que se consegue medir;
- Elevada taxa de acidentes do trabalho, e;
- Serviços de Assistência Técnica após a entrega.
LEAN NA LOGÍSTICA
O transporte de cargas é parte da cadeia de suprimentos – supply chain, que vem crescendo e se adaptando à competição por boas cargas e aumento dos custos.
Para responder a isto, as Transportadoras estão mudando de simples transportadoras para operadores logísticos integrando armazéns e operando em cross docking.
O Lean na Logística visa diminuir os custos e desperdícios, como por exemplo:
- Avarias nas cargas dos clientes por erro da operação;
- Consumo de combustível acima da média recomendada pela fábrica;
- Consumo de pneus por dano acidental ou mau uso;
- Ociosidade de veículos, equipamentos e pessoas;
- Ocupação deficiente do espaço de cargas devido à falta de carga ou erro de carregamento;
- Roteiros não otimizados em termos de tempo, distância e tipos e condições das rodovias.
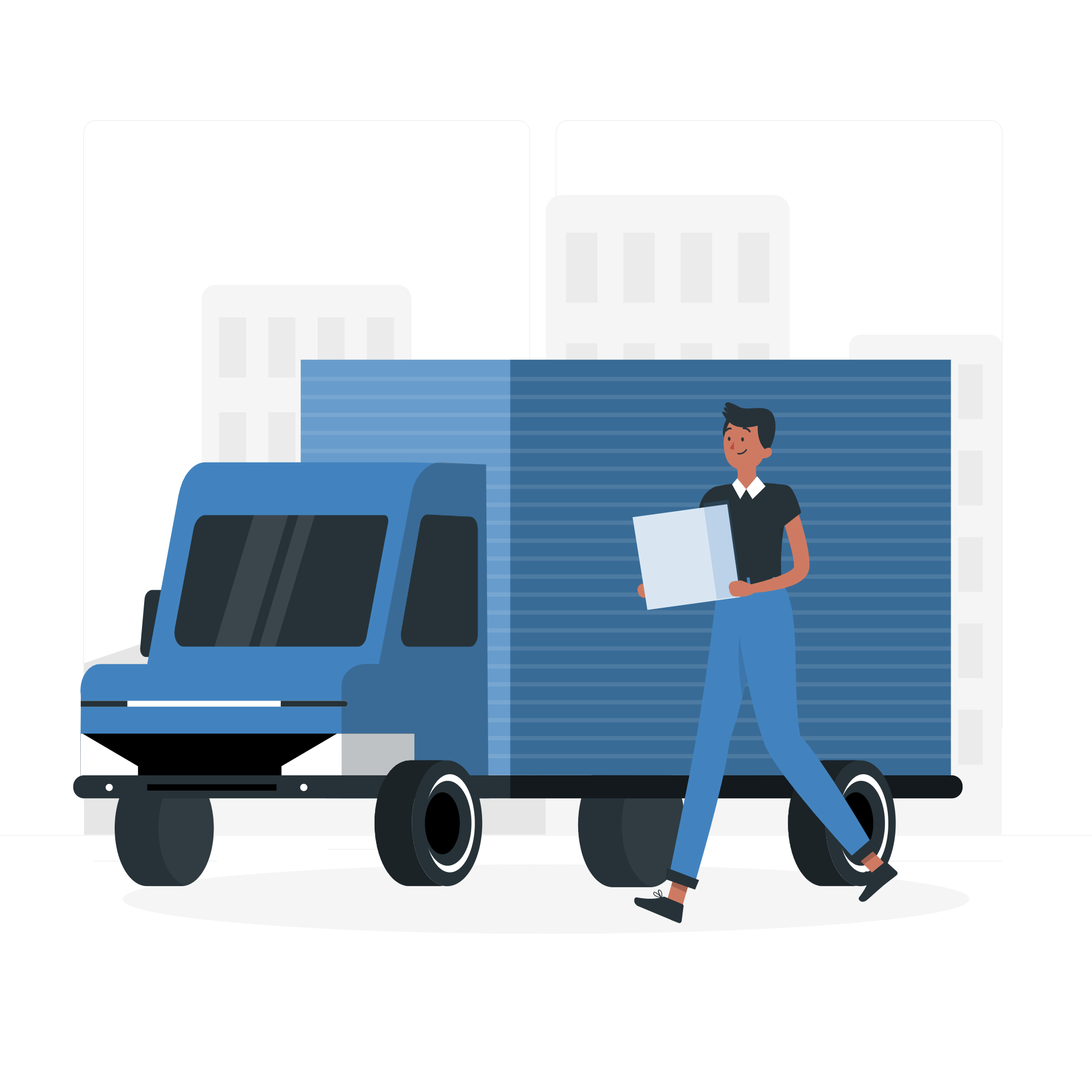
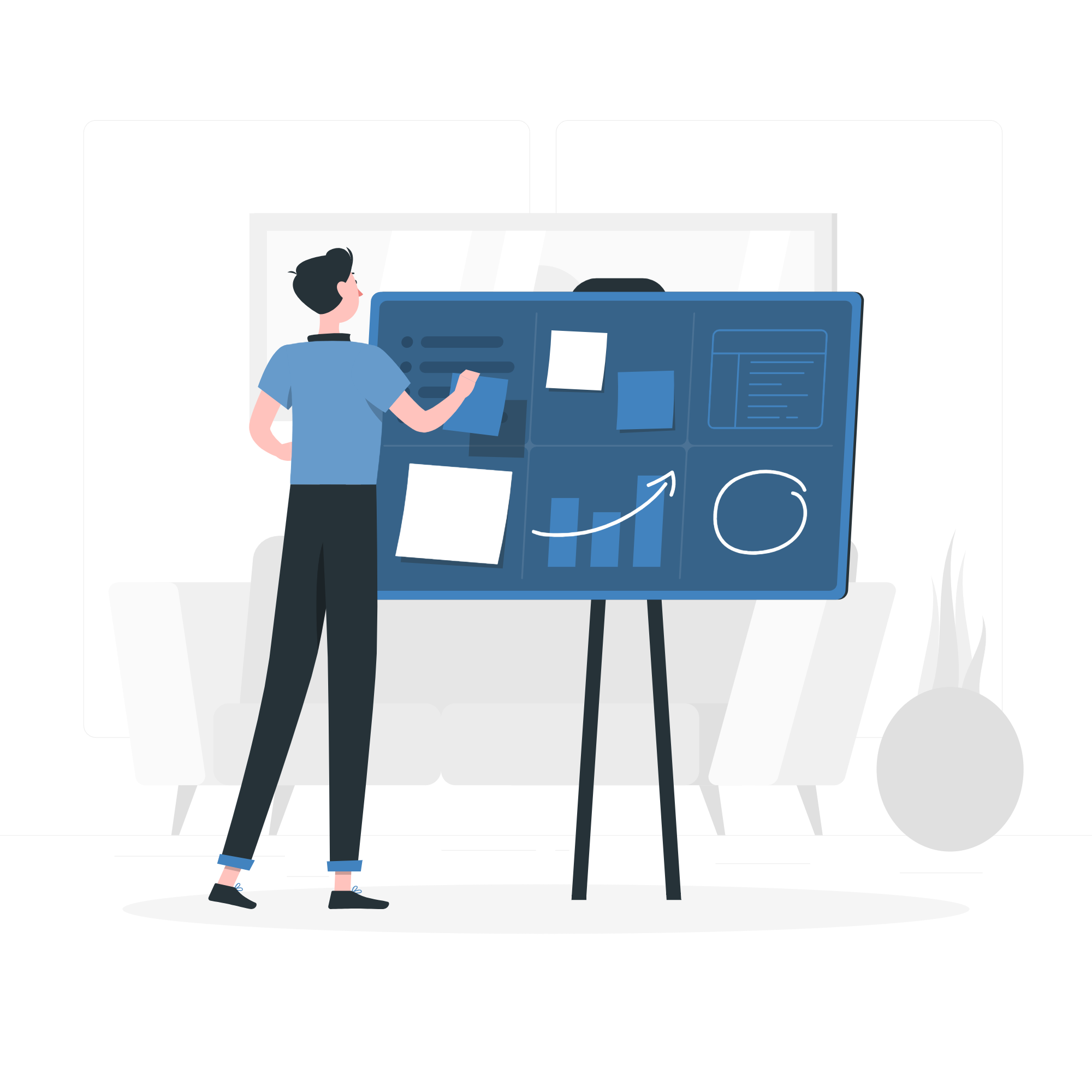
LEAN EM SERVIÇOS ADMINISTRATIVOS
Em muitas empresas os custos, os serviços e a qualidade das atividades administrativas não são visíveis para os clientes, ainda que 80% dos defeitos nos produtos sejam gerados por erros de mau entendimento das necessidades dos clientes e/ou erros de projeto.
O Lean em Serviços busca diminuir os 8 tipos de desperdícios nas atividades administrativas e serviços:
- Superprodução: Geração de documentos antes da próxima pessoa estar pronta para ele ou de serem necessários, compra de itens antes da necessidade;
- Inventário: Processamento de transações e relatórios em lotes, suprimentos de escritório;
- Espera: Sistema inoperante, tempo de resposta do sistema, aprovação por outras pessoas, necessidade de muitas assinaturas, aguardando informações de clientes;
- Processamento adicional: Relatórios e/ou indicadores desnecessários ou excessivos, re-entrada de dados, cópias adicionais, atividades de proteção, relatórios de atividades, atividades de fechamento do mês;
- Correção: Erros de entrada de pedido, erros de projeto, pedidos de mudança de projeto, erros na fatura;
- Excesso de movimentos: Deslocamento de pessoas para buscar, entregar dados e informações;
- Transporte: Excesso de reply nos e-mails, múltiplas passagens de documentos, múltiplas aprovações;
- Sub-utilização de pessoas: Funcionários com limitação de responsabilidades e/ou autoridades sobre tarefas básicas, falta de ferramentas administrativas adequadas, gestão de comando e controle sem delegação.
LEAN EM ALIMENTOS E BEBIDAS
As perdas e desperdícios nas indústrias de alimentos e bebidas ocorrem antes, durante e após o processamento dos alimentos e bebidas, devido a falhas nos processos, e do projeto de gestão de risco da Análise dos Perigos e Pontos Críticos de Controle – APPCC, e dos Programas de Pré-Requisitos – PPR.
Um exemplo de falha do APPCC é a estocagem de mosto de uva para inspeção e testes da sanidade do produto.
Outras falhas além do armazenamento podem ocorrer no transporte de matérias-primas, interrupção da produção, ineficiência de equipamentos e erros humanos.
Como exemplo de perdas devido a falhas de equipamento citamos as perdas no envase de bebidas. Individualmente são apenas alguns ml por garrafa ou embalagem, porém estes poucos ml multiplicados pelos milhares de garrafas diárias ao longo do ano geram milhares de reais em perdas.
A acomodação com as perdas e desperdícios nos vários processos persiste devido ao baixo valor agregado individual dos produtos, facilidade de descarte de produtos impróprios, e a uma falta de cálculo anualizado das perdas e desperdícios individuais dos alimentos e bebidas – São os pequenos grandes números!
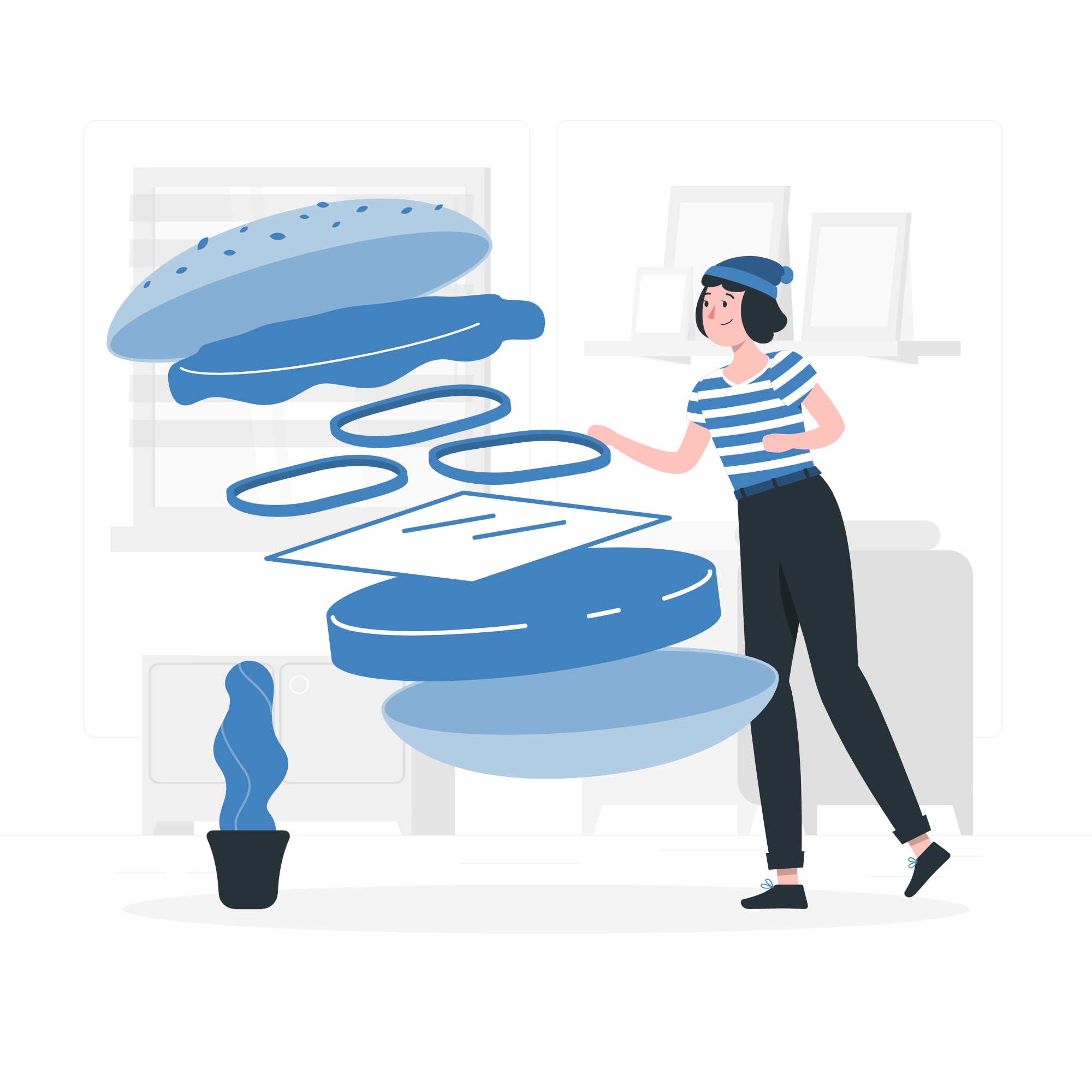
METODOLOGIA LEAN EM PDCA
A sua organização pode contar com o suporte de nossa Consultoria Lean para:
METODOLOGIA LEAN EM FLUXOGRAMA
Veja abaixo como é a metodologia da nossa Consultoria Lean através de um fluxograma:
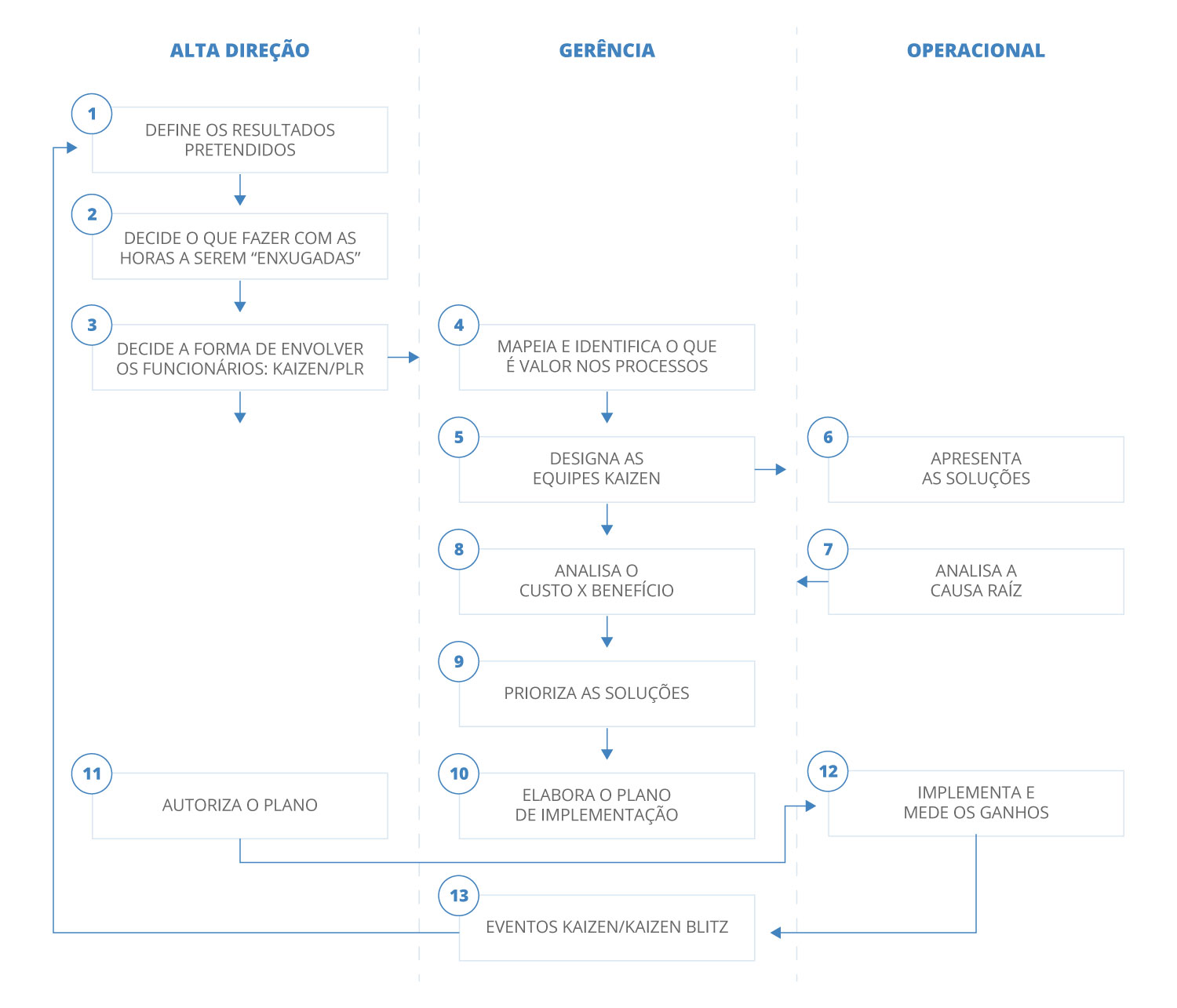
CASE 1 - LEAN ELIMINA O REFUGO DE 80% NUMA LINHA DE MONTAGEM
Veja abaixo um exemplo de uma solução para guiar a aplicação de adesivos em cones para colar calotas de alto-falantes ovais (6 x 9) e que resultou na eliminação de um refugo em 80% na linha de montagem:
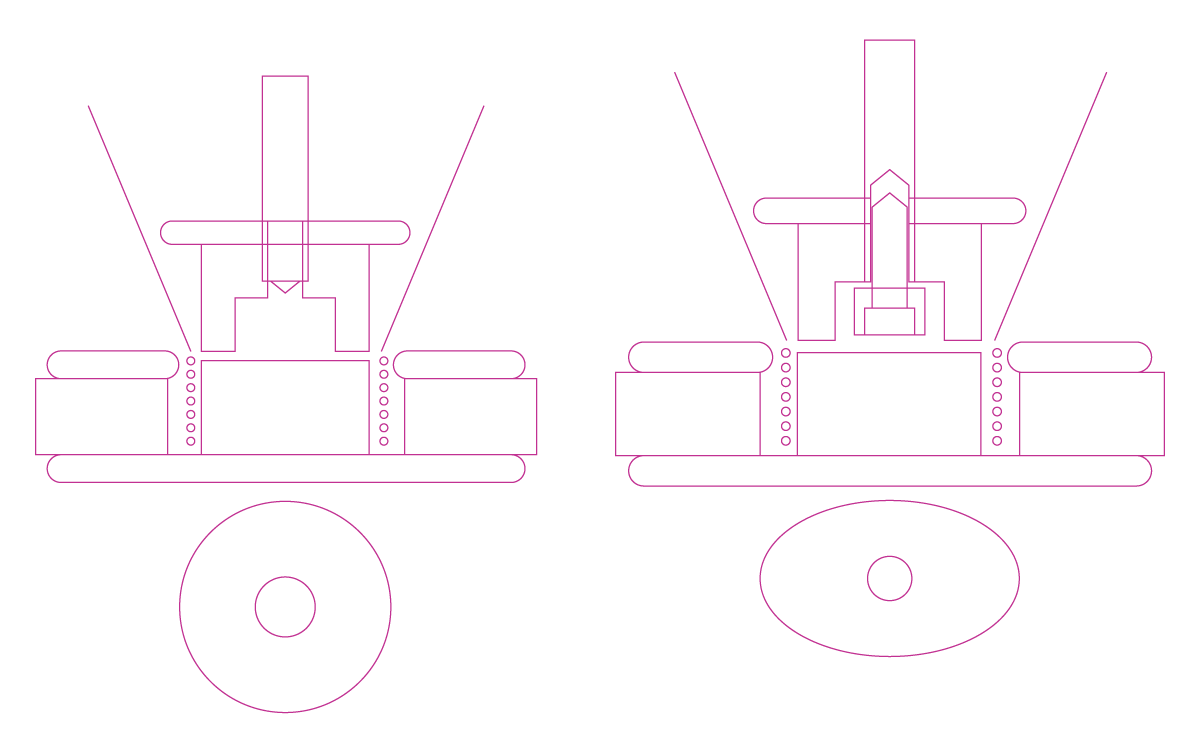
A solução foi desenvolver um dispositivo de guia para os bicos de cola semelhante aos já utilizados nos alto-falantes redondos com duas diferenças, a guia para o bico de cola era oval e o conjunto centralizador tinha um parafuso Allen que podia ser ajustado pelas pessoas da montagem para regular a força magnética sobre o dispositivo, que devia ser forte o suficiente para não deixá-lo sair da posição, mas leve para poder colocá-lo e tirá-lo da centralização no conjunto magnético evitando esforços excessivos.
Como consequência, a rejeição nos testes acústicos caiu a zero e a linha de “desmontagem” para o retrabalho foi eliminada.
Observação: Os funcionários da linha de desmontagem não foram demitidos e sim distribuídos entre os outros processos como Pintura e a própria Montagem, uma vez que muitas pessoas eram mais habilidosos para desmontar do que as que montavam.
CASE 2 - LEAN REDUZ O LEAD TIME DE 3 MESES PARA 30H
A empresa em questão produzia tinha um lead-time de 3 meses, sendo 1 mês para realizar as compras, 1 mês para fabricar os componentes e 1 mês para montá-los. Isto dificultava o atendimento das Vendas pois “sobrava o que não precisava e faltava o que era necessário”.
As vendas de alto-falantes profissionais com forte sazonalidade de Dezembro a Fevereiro ficavam longe de serem atendidas gerando um stress organizacional pela perda de oportunidade do valor agregado de cada alto-falante cujo pagamento era à vista.
Soluções normais de aumento do quadro produtivo não eram suficientes para atender as súbitas oportunidades de final de ano, até pela inércia de contratação e treinamento da mão-de-obra.
Soluções mais elaboradas, como otimização dos tempos nas linhas de montagem, passando de 200 para 800 alto-falantes diários, dispositivos poka-yoke, sistema de troca rápida de ferramentas possibilitaram reduzir o lead-time de 3 meses para 3 semanas, mas ainda assim não eram suficientes para atender a forte sazonalidade.
A solução consistiu em analisar as projeções de vendas, simular as cargas-máquinas para identificar gargalos, fazer estoques de 2 peças estratégicas de baixo custo e buscar fornecedores a quem foi dado conhecer os números previstos com o compromisso de abastecimento.
Chegado o final de ano, as vendas dos alto-falantes profissionais começaram a acontecer. Às 12h00 o Comercial fechava os pedidos do dia, o PCP informava aos fornecedores a quantidade de componentes necessários que eram entregues até as 18h00 do mesmo dia.
Na sequencia os componentes eram lavados e pintadas durante o turno da noite e às 8h00 do dia seguinte entravam nas linhas de montagem para serem faturadas e despachadas até às 17h00.
Um lead-time de 30h00, inimaginável, quando comparado ao lead time inicial de 3 meses!
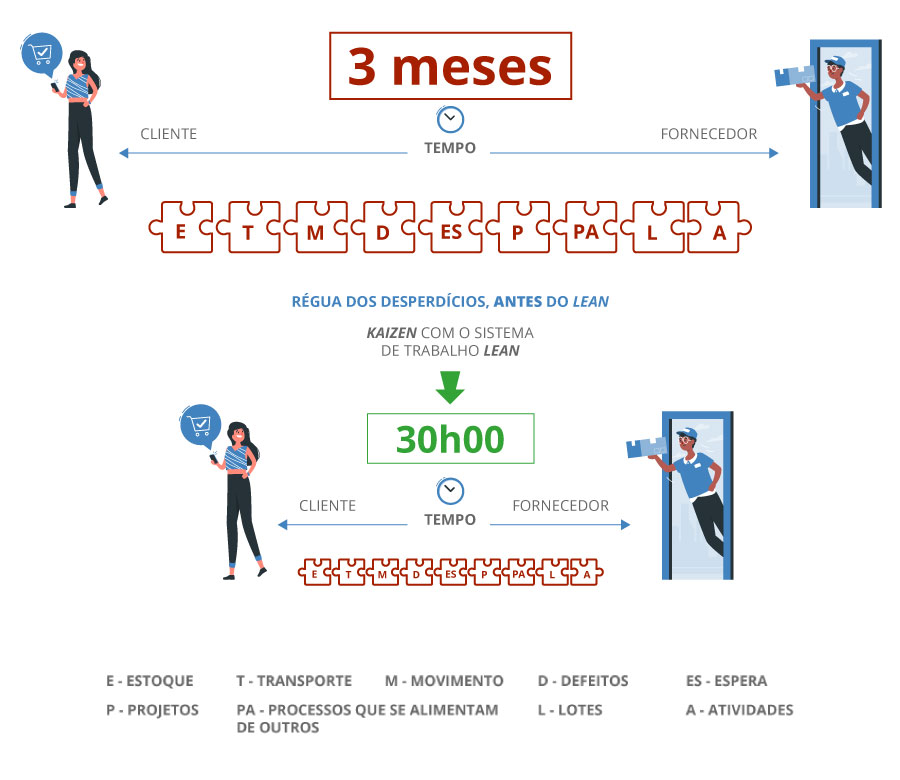
O nosso serviço não é gerar resultados expressos em números!
Precisa de um suporte para planejar, executar, analisar ou fazer um upgrade na sua jornada Lean?
Entre em contato conosco através do formulário, ou telefone 51 9 9985 9473 | 51 9 9961 2192 | 51 3347 7819 e e-mail sergio@konrad.com.br
POR QUE CONTRATAR A NOSSA CONSULTORIA LEAN
Transmitimos a experiência de:
- Liderar equipes e melhoria;
- Obter resultado no GEMBA (chão de fábrica);
- Medir os resultados em números.
Conheça nossoa perfis no Linkedin.
A Konrad ganhou a confiança de Clientes de todos os tamanhos.
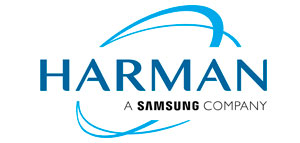
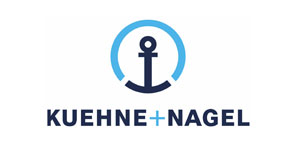
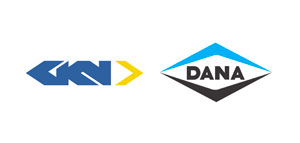
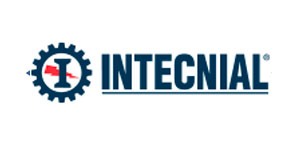
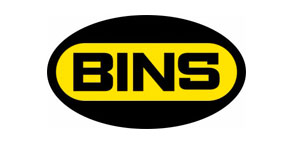
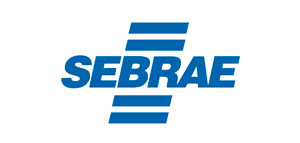
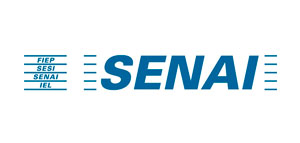
Deixe aqui suas dúvidas, críticas e comentários: